Strip
Schleuniger AG
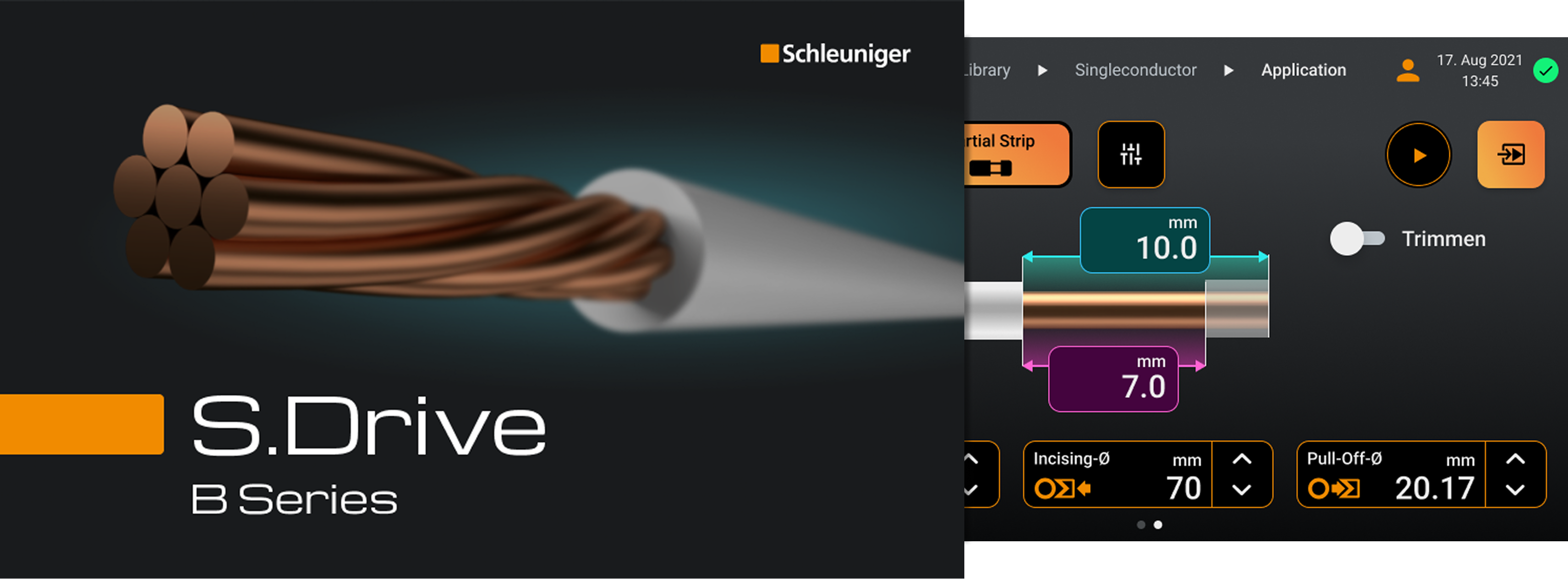
The purpose of a Schleuniger stripping machine is to efficiently and accurately remove insulation from electrical wires and cables, enhancing productivity, precision, and safety in industrial applications
DESIGN OBJECTIVES
CHALLENGES
Enhancing Usability for Complex Tasks
Reducing errors, streamlining workflows, increasing efficiency
Catering to a Diverse User Base
Accessibility for all users, minimizing the need for extensive training
or support
Increasing Automation and Integration
Navigating complex integrations without feeling overwhelmed
Standardising Interfaces across Product lines
Creating a unified design language to improve consistency, brand
identity, and ease of use across Schleuniger’s ecosystem
Balancing Complexity with Simplicity
Simplifying workflows while retaining advanced functionality
required by expert users for fine-tuned stripping adjustments
Integration with Existing Systems
Ensuring compatibility with older machine models, enterprise
software, and connected devices without compromising usability
Catering to Diverse Personas
Designing for a wide range of users, from seasoned engineers to
first-time operators, without alienating either group
Ensuring Stripping Precision and Quality Control
Providing clear feedback on stripping performance, handling
different wire types, and avoiding damage to conductors
Efficient article programming
We designed the UX for the Schleuniger B300 with a strong focus on usability, efficiency, and adaptability, ensuring smooth operation on a compact 5-inch screen. Our goal was to create an intuitive interface that minimizes unnecessary steps while providing operators with full control over cable management, material configuration, and processing settings.
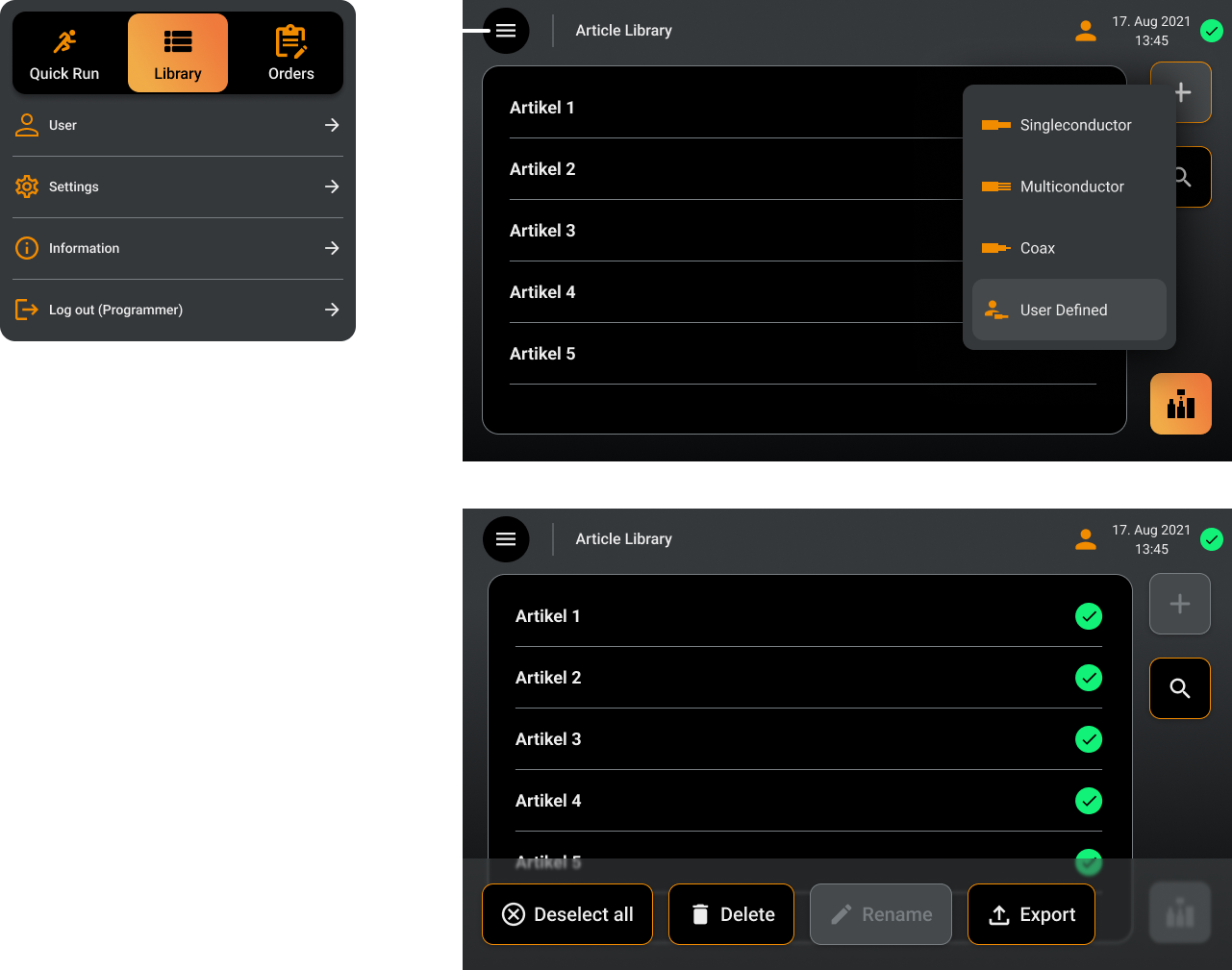
1. We carefully structured the layout to make the most of the limited display area, ensuring all essential functions are easily accessible without clutter.
2. We introduced a long-press feature, allowing users to quickly modify the cable library without the need for extra buttons, making interactions smoother and more intuitive.
3. We used contrast, icons, and structured lists to help users quickly find and manage articles, reducing cognitive load.
4. We logically grouped essential functions—selection, renaming, exporting, and deleting cables—so users can complete tasks efficiently with minimal effort.
5. We ensured that interface elements follow familiar design patterns, enabling users to navigate the system without extensive training.
We designed an intuitive and efficient interface that allows users to configure raw materials and program processing parameters in real time. Our goal was to provide maximum flexibility while keeping the interface clean and easy to navigate.
1. We made it possible to switch between single-conductor and multi-conductor cables in real time, ensuring seamless workflow adjustments.
2. We implemented a feature that allows users to change the cable color, improving identification and traceability.
3. We ensured that cable dimensions, such as diameter and other key parameters, can be modified directly from the interface, allowing for quick and precise adjustments.
4. We allowed users to switch between full and partial stripping instantly, adapting to different processing needs without workflow interruptions.
5. We created a dedicated function that enables users to generate a test sample and verify all parameters before starting production, minimizing errors and material waste.
6. We placed the most essential controls on the main screens for quick access, while secondary settings are neatly organized under menu buttons, keeping the interface uncluttered and user-friendly.
With this approach, we ensured that operators can configure and adjust cable processing settings quickly and efficiently, improving both speed and accuracy in production.
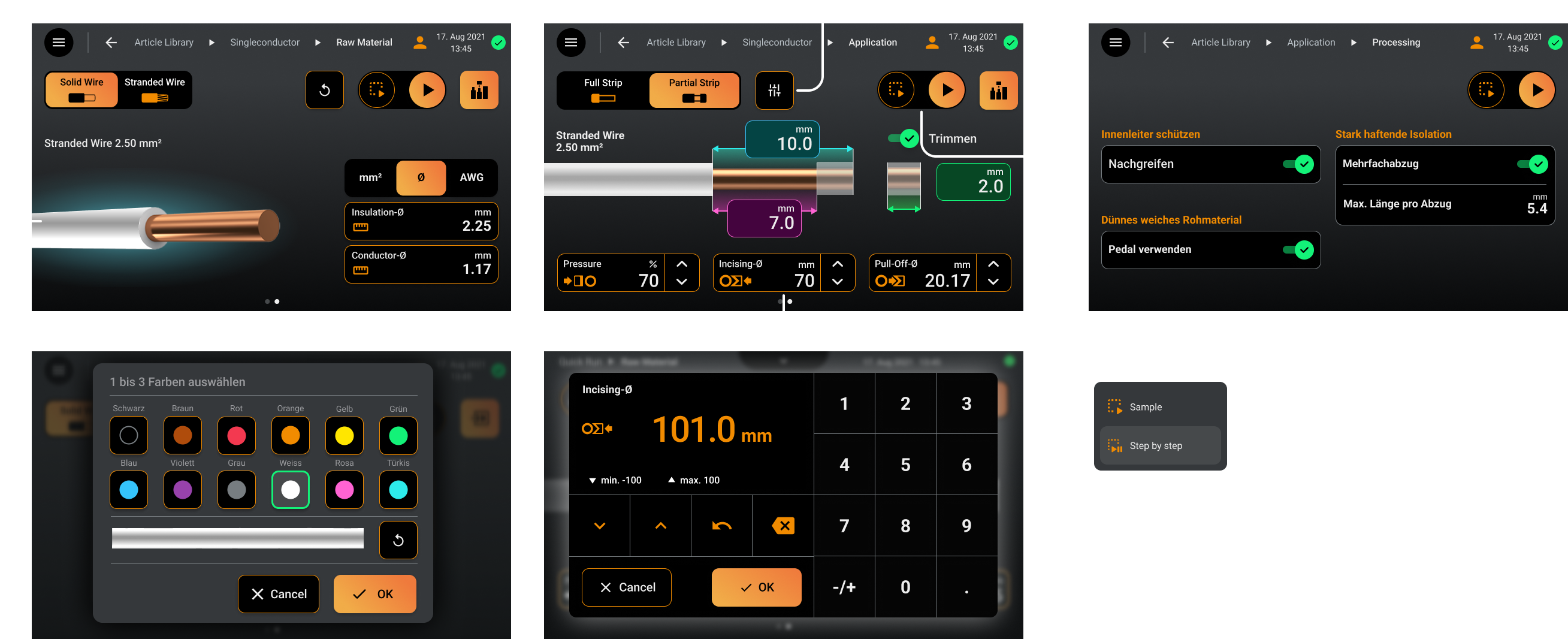
Production and Quality Control
We designed the Production Page for the Schleuniger B300 to provide operators with a clear, structured workflow while ensuring flexibility in cable processing. This interface allows users to monitor and adjust production in real time, ensuring efficiency and accuracy.
1. Operators can choose between Sample Production, Standard Production, and Step-by-Step Mode, allowing for full control over the process. Sample Production enables users to test a single cable before mass production. Step-by-Step Mode is useful for verifying each stage before proceeding.
2. The interface displays the current cable being processed and the next one in the queue, ensuring operators always know what’s being worked on.This prevents mistakes and ensures that the correct cable type is being processed at the right time.
3. By tapping on a cable in the list, users can instantly access the cable configuration page, allowing them to modify processing parameters without interrupting production. This ensures that any last-minute changes can be made seamlessly.
4. The left panel allows users to configure job settings, including the number of cables to be produced. It provides an overview of rejected parts, giving operators insight into production quality and allowing them to take corrective actions if needed.
By combining clear visual feedback, easy access to key functions, and flexible production modes, we ensured that the Production Page delivers a smooth, user-friendly experience for operators working with the Schleuniger B300.
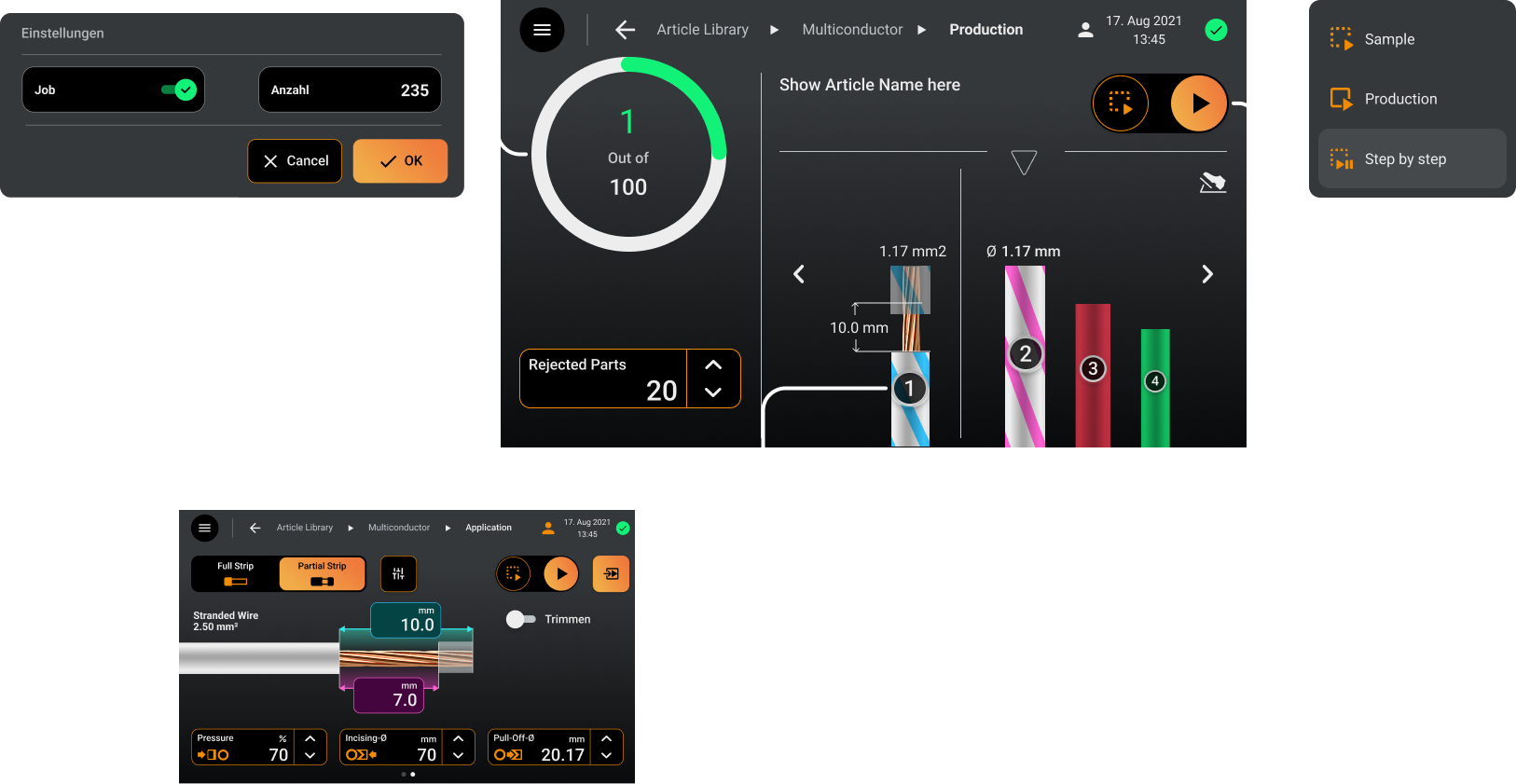
Tailored Processing Solutions
We developed a flexible and unified UX for handling different types of cables in the Schleuniger B300. The interface accommodates a variety of cable types, including:
• Single-Conductor Cables • Multi-Conductor Cables • Coaxial Cables • User-Defined Cables with custom layers
For each type of cable, we designed a unique solution that balances customer needs with machine capabilities. The interface dynamically adjusts to ensure that all necessary configurations are available while keeping interactions intuitive.
Despite the different processing requirements, we ensured that the core design remains consistent across all cable types. This approach allows users to:
1. Quickly adapt to different cable configurations without a steep learning curve.
2. Easily navigate the system thanks to familiar UI patterns and controls.
3. Maintain workflow efficiency by reducing cognitive load and unnecessary complexity.
By combining customized functionality with a harmonized design, we created an interface that provides both flexibility and ease of use, making cable processing smoother and more efficient.
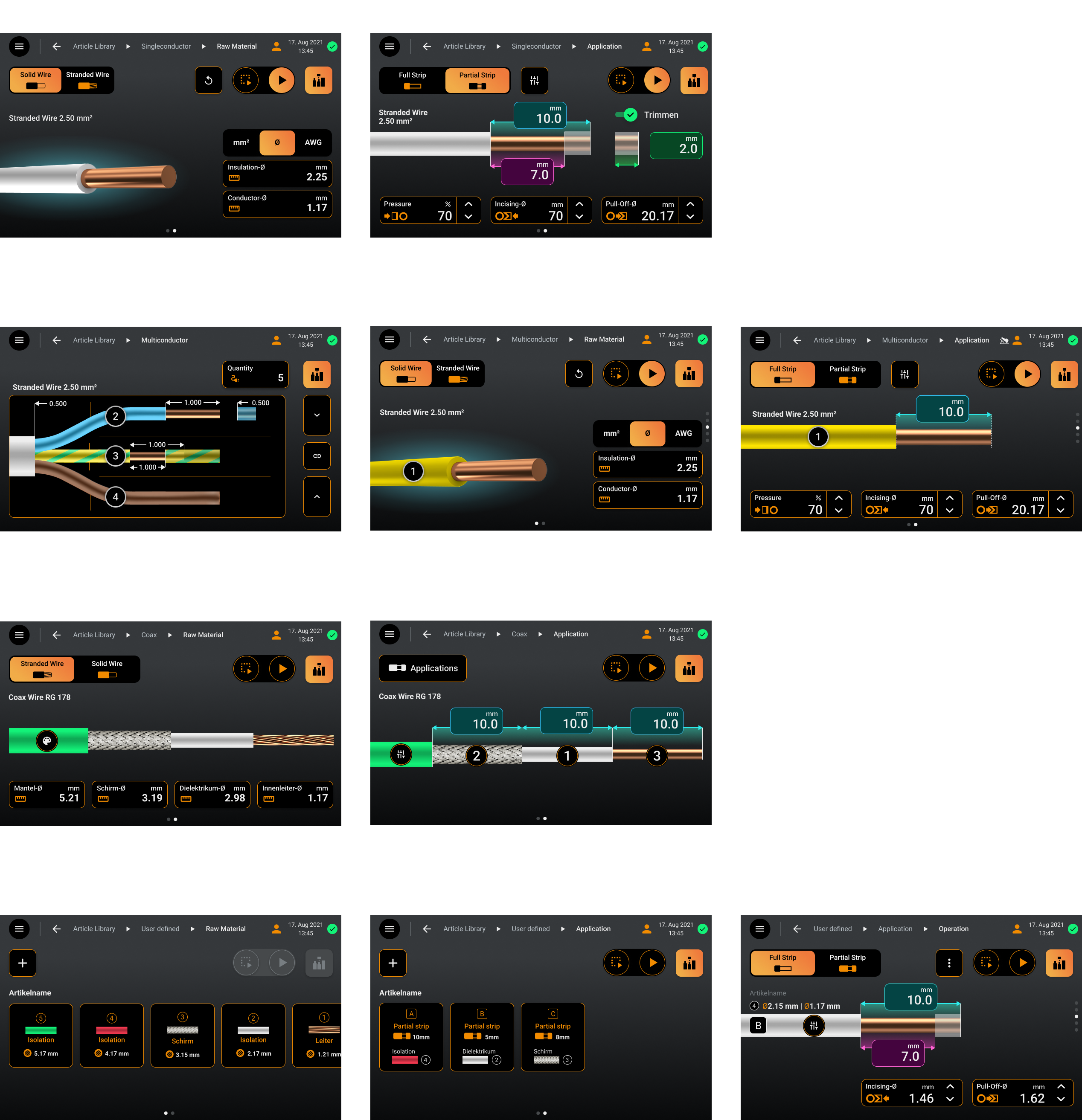
colours and typography
The interface employs sharp contrasts to highlight key features and controls, ensuring that users can navigate the software with ease. A dark background was chosen for the software interface, harmonizing with the machine’s dark exterior. This not only enhances readability and reduces eye strain but also reinforces the sleek, professional appearance of the machine
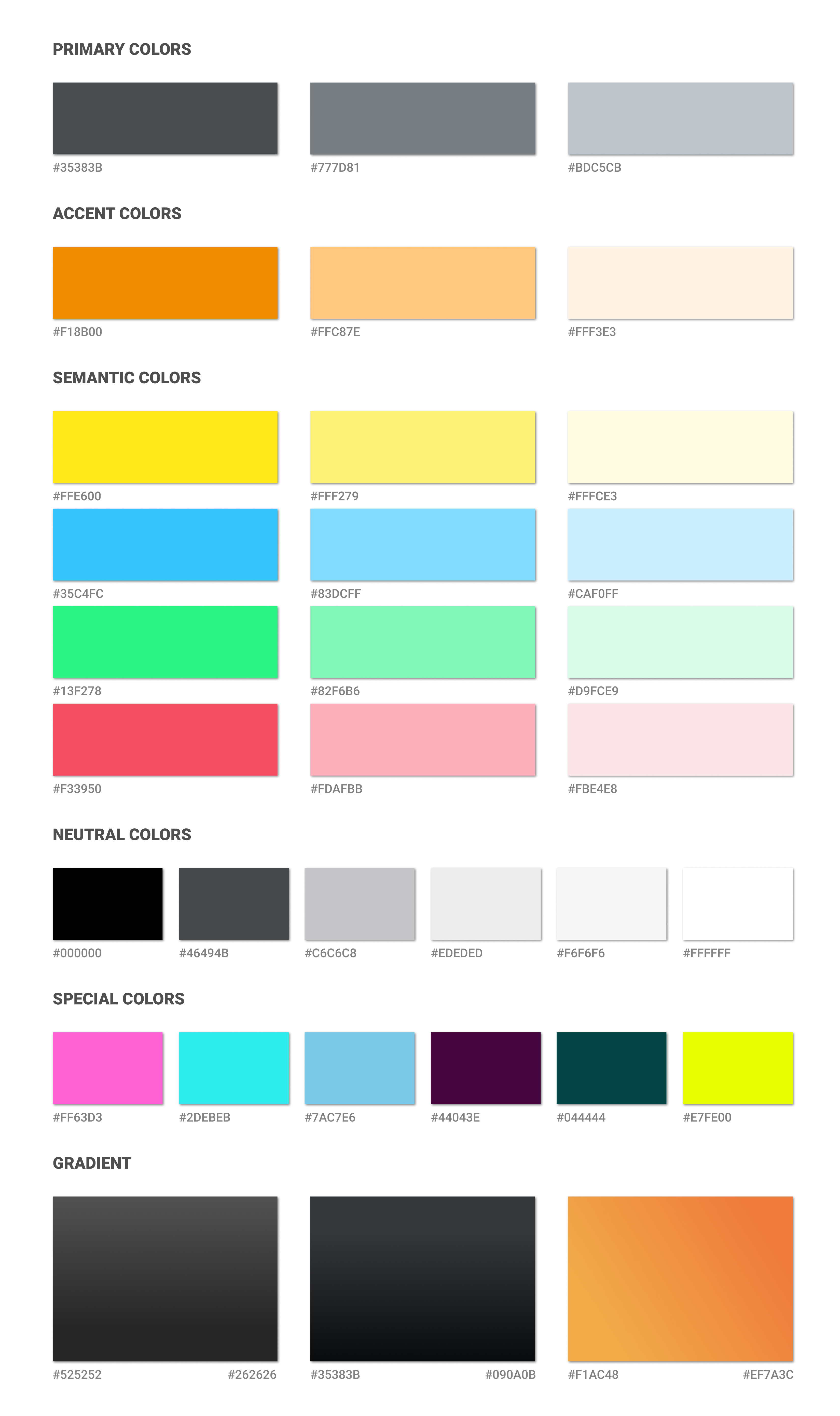
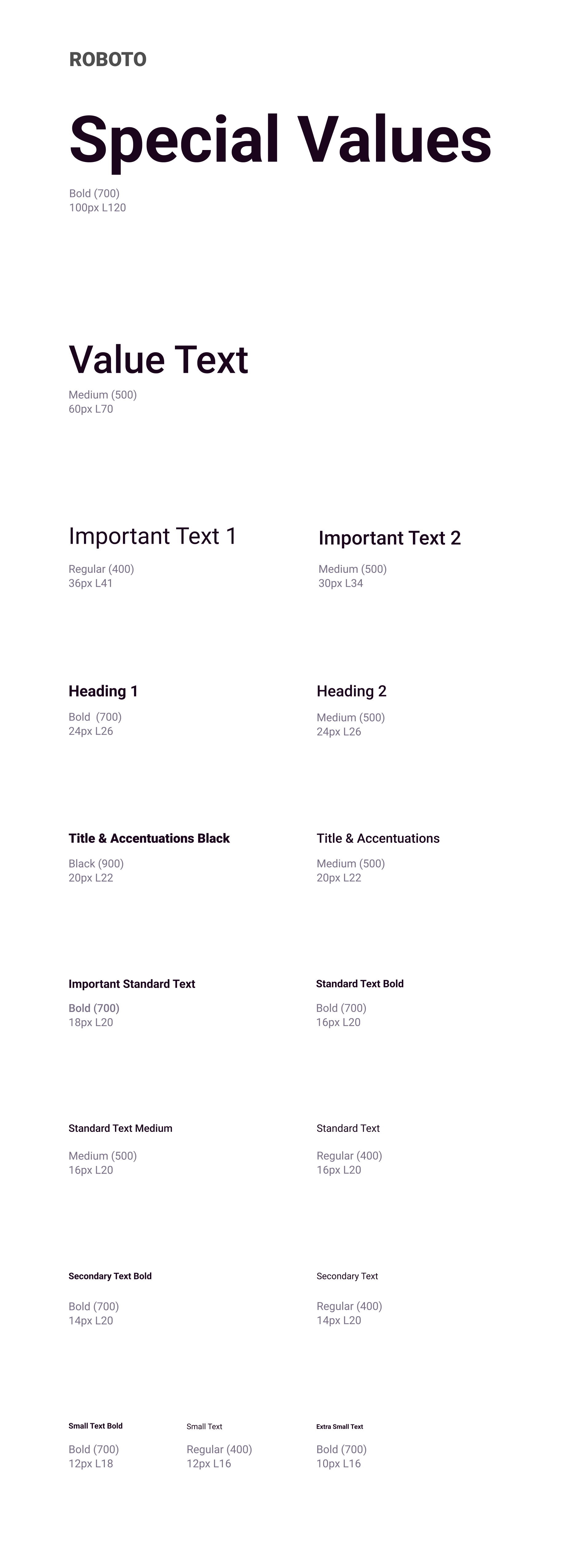