Cut & Strip
Schleuniger AG
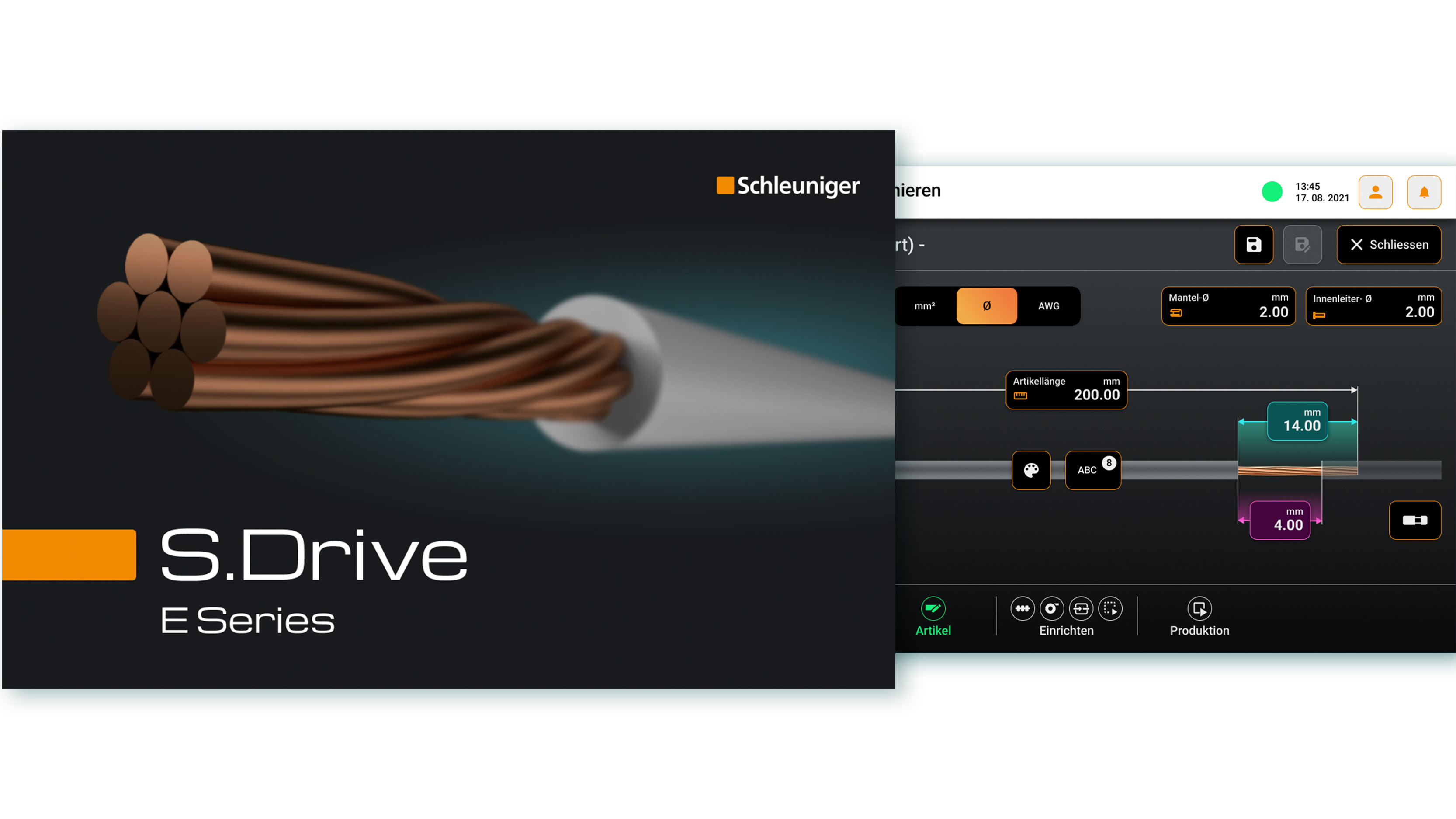
Schleuniger’s Cut & Strip machines are designed for the precise cutting and stripping of wires and cables. These machines serve a crucial purpose in industries such as automotive, aerospace, telecommunications, and electronics, where accurate wire preparation is essential for ensuring proper connections and functionality in electrical systems.
The system of a cable processing machine is highly complex and requires deep professional knowledge. Without the necessary experience and training, operating such a system can be challenging. Our goal as UX designers was to create an intuitive interface that allows even users without specialized education to work efficiently and without errors.
DESIGN OBJECTIVES
CHALLENGES
Enhancing Usability for Complex Tasks
Reducing errors, streamlining workflows, increasing efficiency
Catering to a Diverse User Base
Accessibility for all users, minimizing the need for extensive training
or support
Increasing Automation and Integration
Navigating complex integrations without feeling overwhelmed
Standardizing Interfaces Across Product Lines
Standardizing and unifying the design creates consistency,
improves brand identity, and simplifies learning for users working
across multiple products
Adapting to Modern UX Expectations
Aligning with the best practices of modern design, offering
touch-friendly interfaces, responsive designs, and visually
appealing layouts
Balancing Complexity with Simplicity
Simplifying workflows without sacrificing the advanced functionality
needed by expert users
Integration with Existing Systems
Integration with the company’s ecosystem, including older machine
models, enterprise software, and other devices, while maintaining
usability
Catering to Diverse Personas
Users may range from seasoned professionals to new operators.
The design must cater to both ends of the spectrum without
alienating either
Technical Constraints
The hardware and embedded systems in these machines impose
limits on the software’s capabilities, making it a challenge to design
within these constraints while maintaining a high-quality user
experience
Real-time cable configuration
In the first step, the user defines all the key characteristics of the final cable:
• Length • End processing type • Color • Markings or printed information • Cable type
To enhance visual clarity and user experience, we integrated a 3D visualization of the cable. As users modify parameters, the cable’s appearance updates in real time, allowing them to see exactly how their changes affect the final product. This dynamic preview ensures better decision-making and reduces the likelihood of errors.
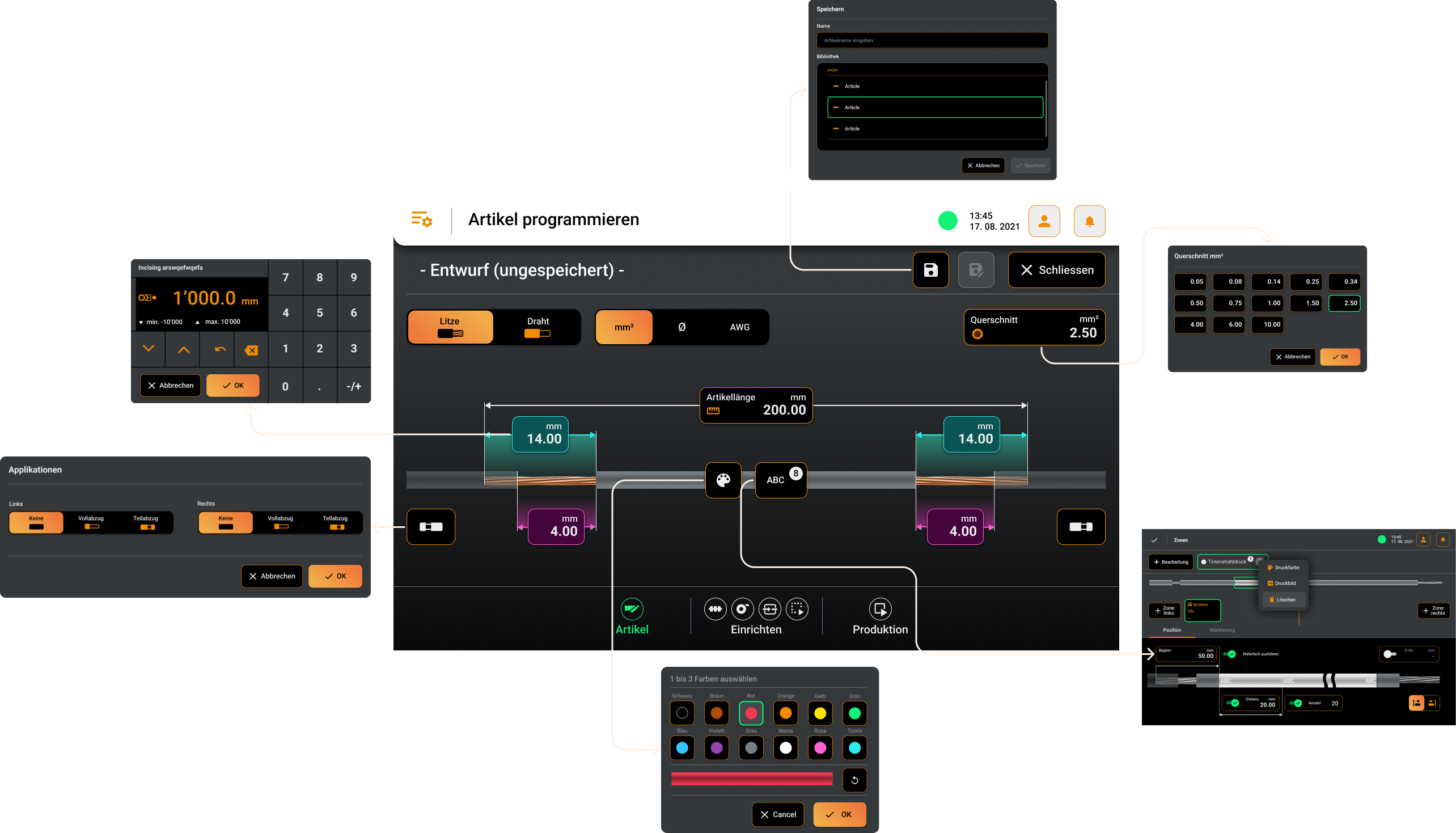
Intuitive navigation system
We implemented a navigation system that reflects the natural workflow and consists of three key stages:
1. Cable Programming – defining the essential parameters such as length, end processing, color, and markings.
2. Settings and Preparation – configuring additional equipment, checking raw materials, loading the cable, creating a test version, and verifying processing quality.
3. Production – the final stage, where serial manufacturing begins.
To keep the interface clean and user-friendly, the SetUp tab is initially collapsed. This way, the user immediately understands that after programming the cable, they will need to configure settings. However, the details of these settings only become visible once the user clicks on the SetUp tab.
The system is designed to guide the user intelligently:
• If certain settings are unnecessary for the specific cable type, the system automatically skips irrelevant steps and directs the user to the appropriate screen.
• If any critical settings are missing, the system prevents further progress, ensuring that all essential configurations are completed before moving forward.
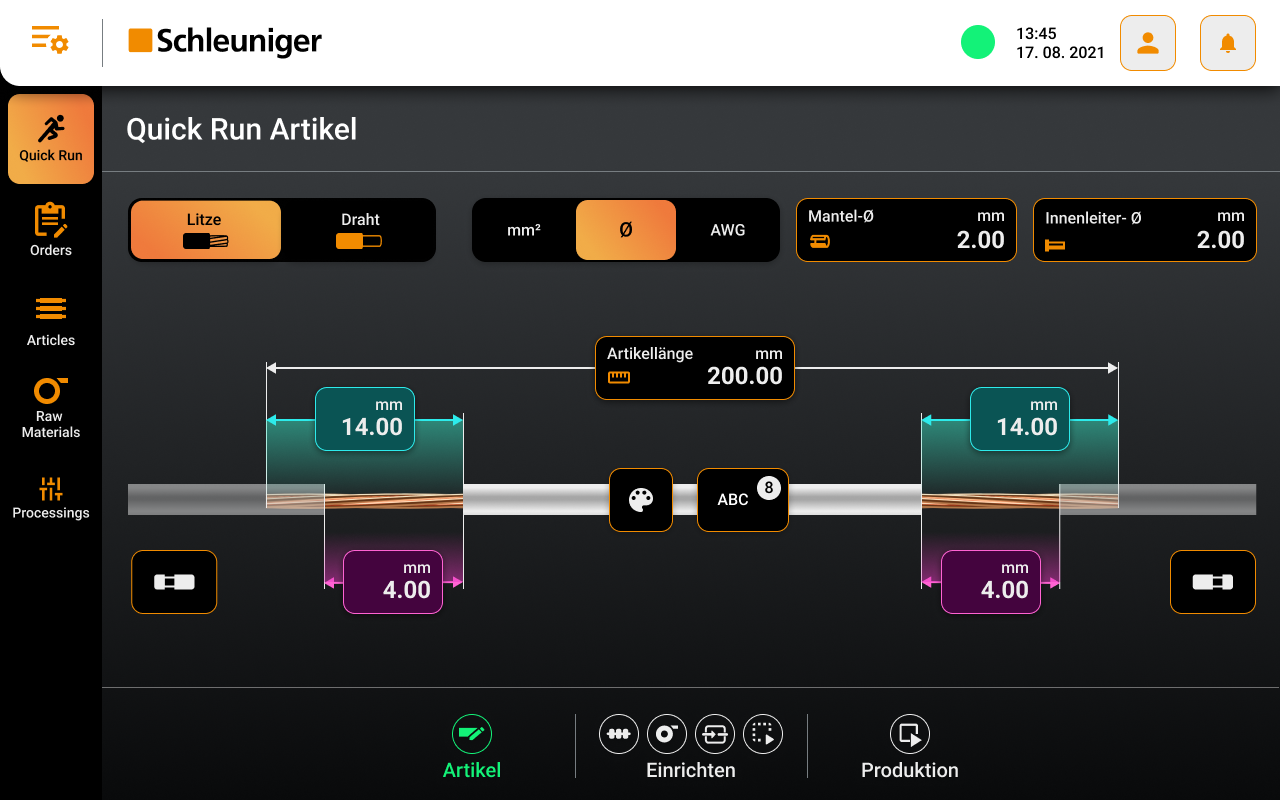
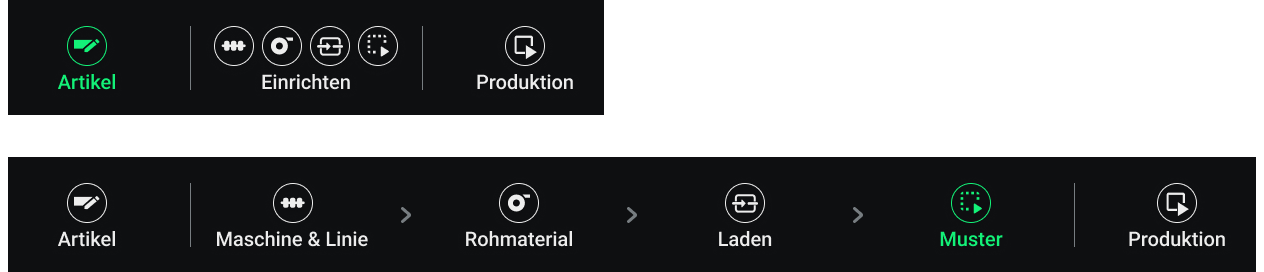
Smart Equipment Management
This interface simplifies the configuration of additional equipment in automated production processes. To ensure seamless operation, the system visually presents all available auxiliary machines in an intuitive card-based layout. Each machine can be activated or deactivated based on current production needs, allowing for flexible adaptation to different workflows.
When a machine is required, the system provides clear, step-by-step instructions on the necessary setup and tasks. Users receive a specific action item related to the selected equipment, such as connection, calibration, or function testing. Only after confirming task completion can they proceed to the next step, ensuring that each piece of equipment is correctly configured before production continues.
This structured and interactive approach enhances efficiency, reduces setup errors, and streamlines the overall production process, making complex machine integration user-friendly and precise.
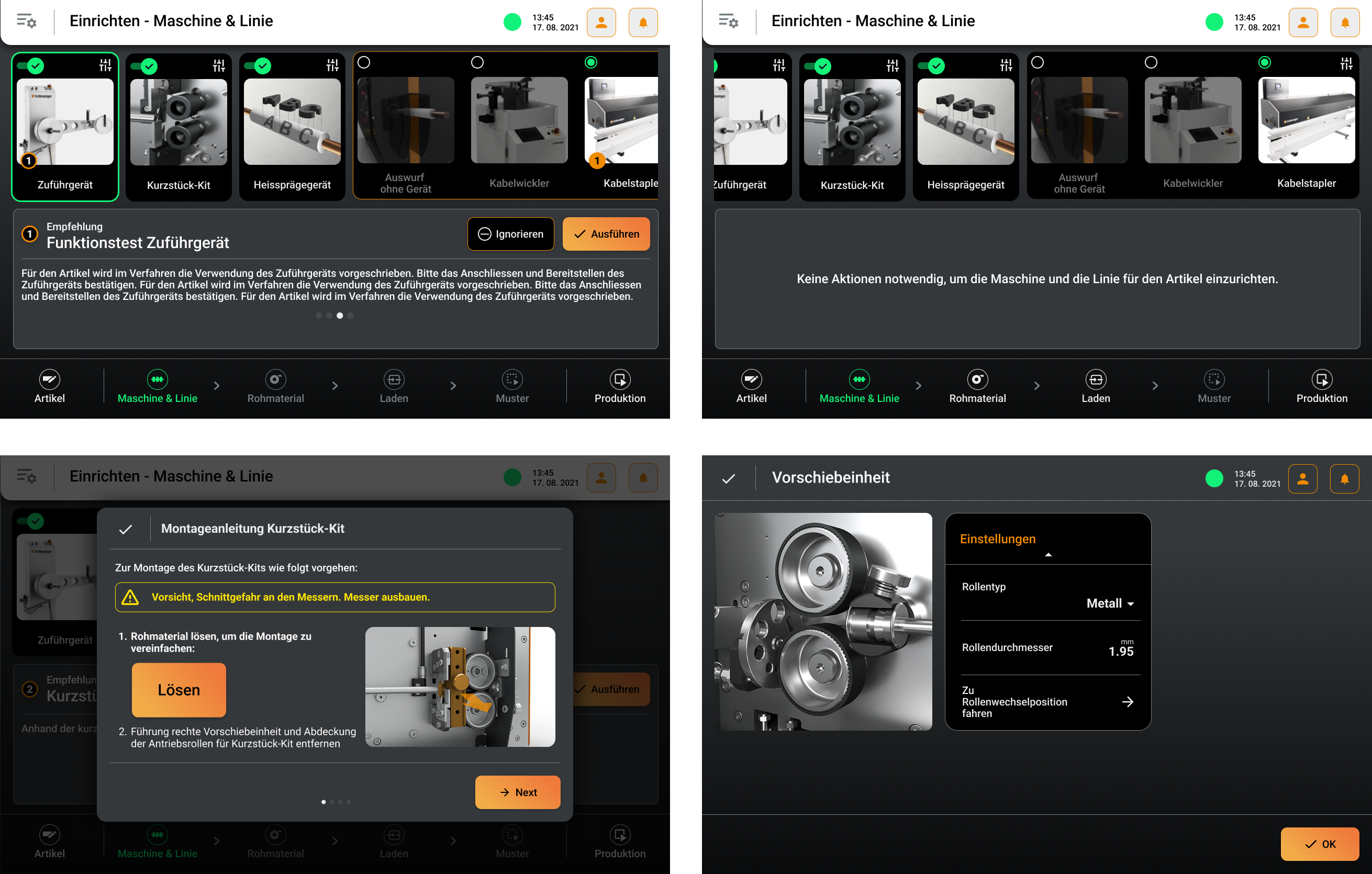
Unique solution for Trouble shooting
A cable processing machine is a highly complex system that demands specialized knowledge. Before beginning full-scale production, users often need to create a sample variant to ensure everything meets the required specifications. If the sample falls short, adjustments to the system settings become necessary. But which settings should be modified?
To streamline the user’s workflow and provide effective guidance, we have developed the “Corrections and Troubleshooting” feature, designed to simplify this process and enhance efficiency.
In the event of an incorrect cable processing result, the system provides an intuitive way for the user to quickly diagnose and resolve the issue. After inspecting the cable, the user selects the side where the processing error occurred—for example, the left-side application. A pop-up window then appears, presenting various troubleshooting options.From a dropdown menu, the user identifies the specific issue—for instance, residual insulation left on the blade. The system then suggests precise adjustments, such as increasing the air blow to clear excess material. These intelligent recommendations help the user fine-tune machine settings effortlessly.
Once the necessary adjustments are made, the user runs a sample test to verify the improvement. This streamlined troubleshooting process ensures minimal downtime, optimized machine performance, and consistently high-quality results.
Information architecture
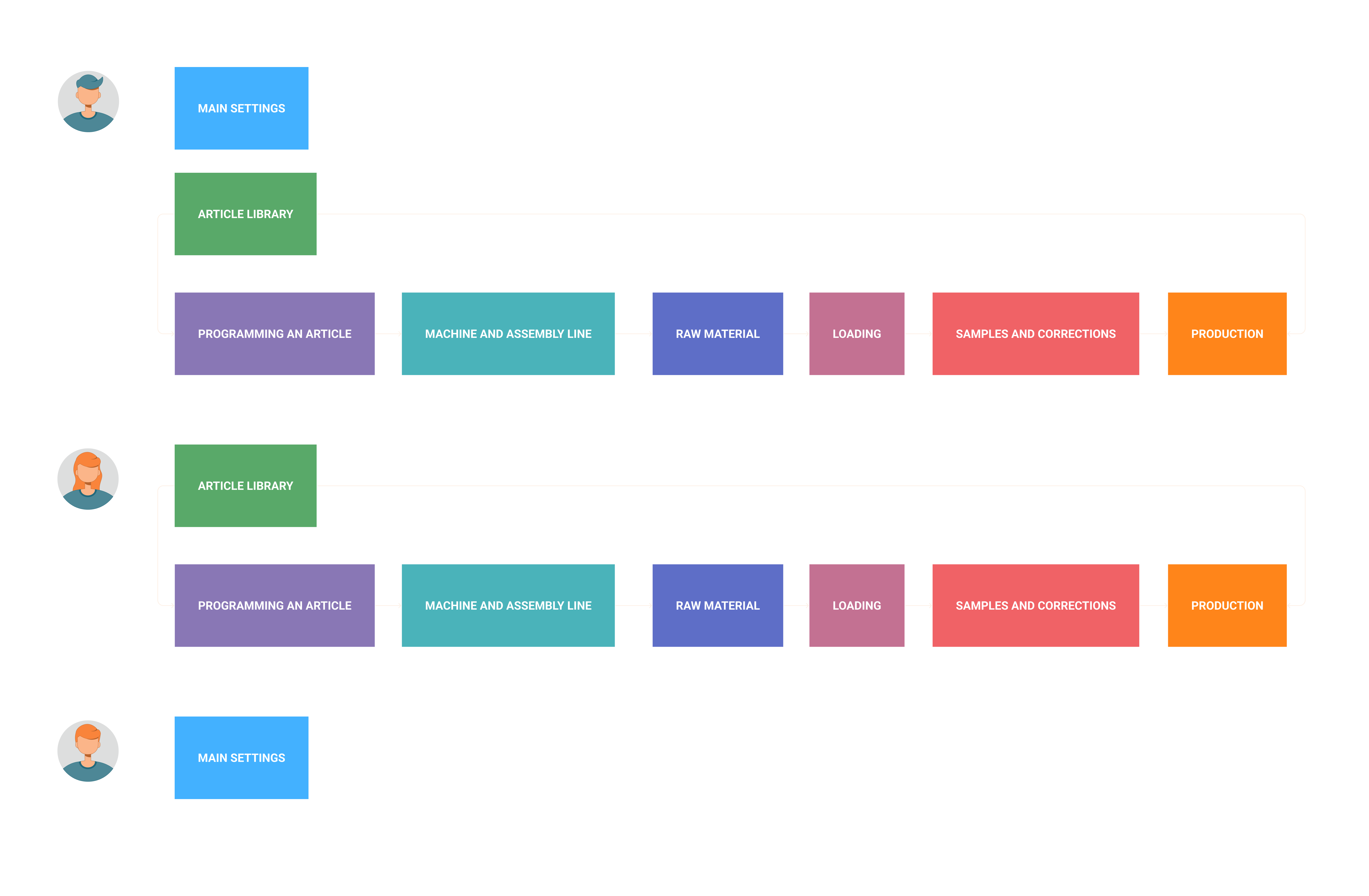
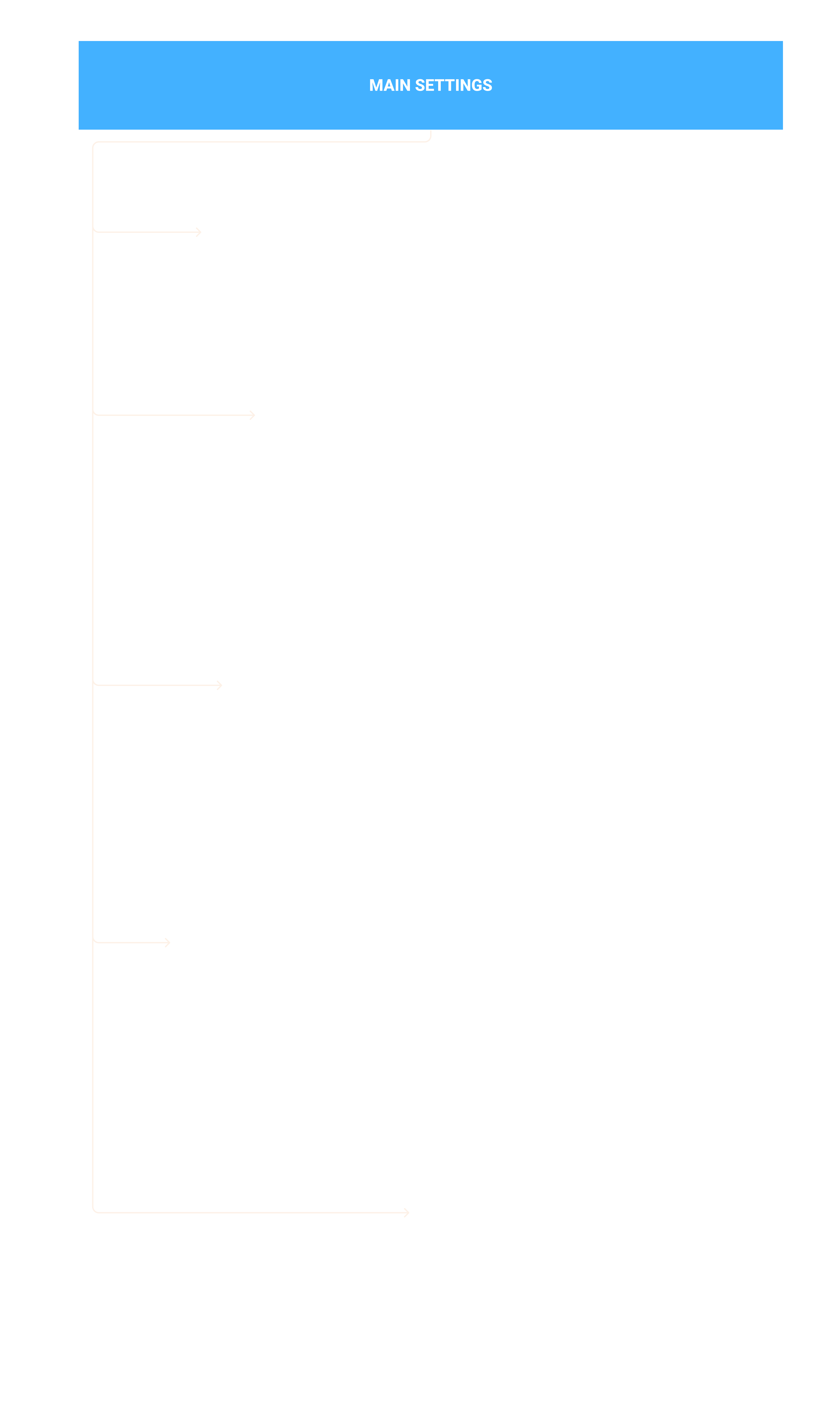
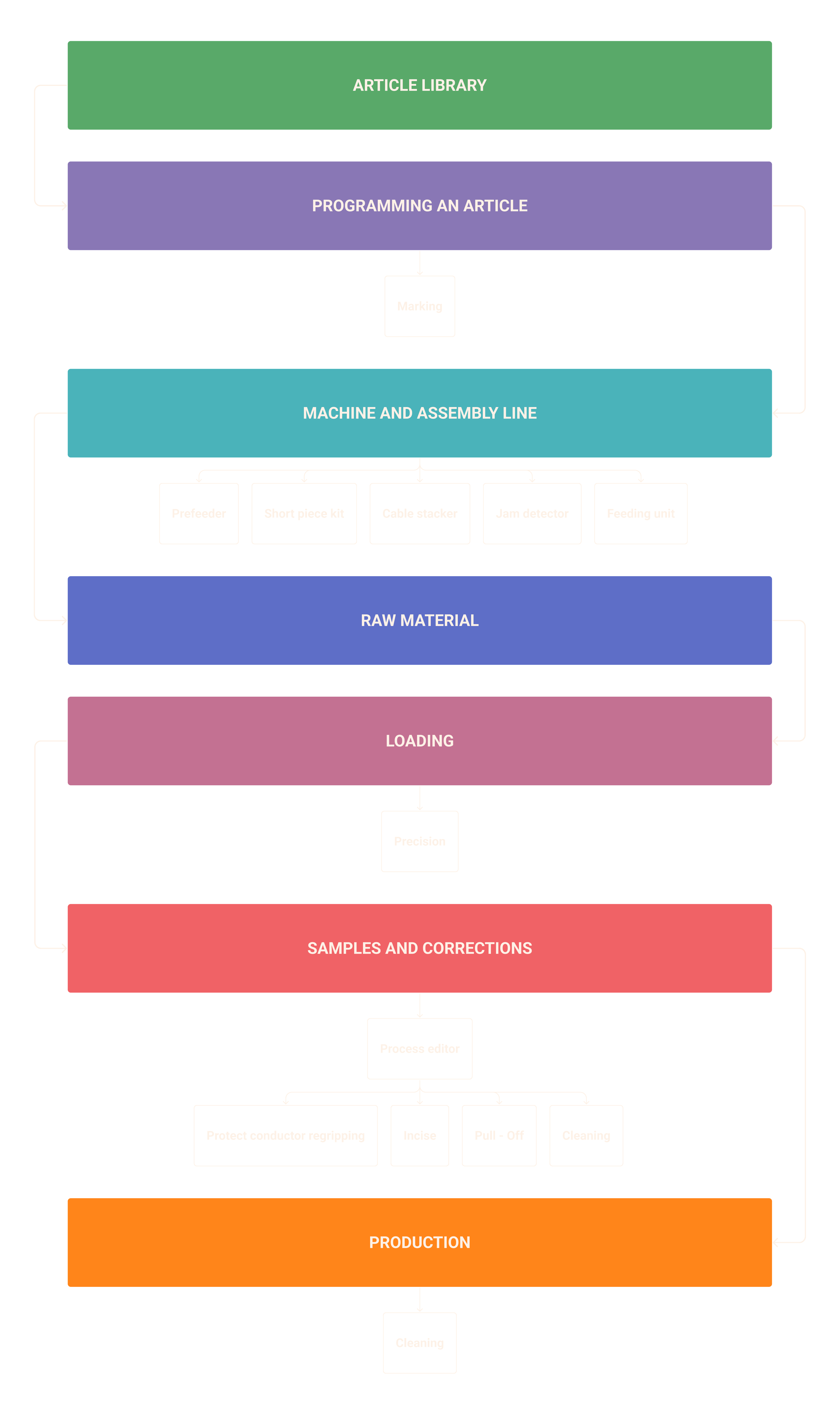
Layout and spacing
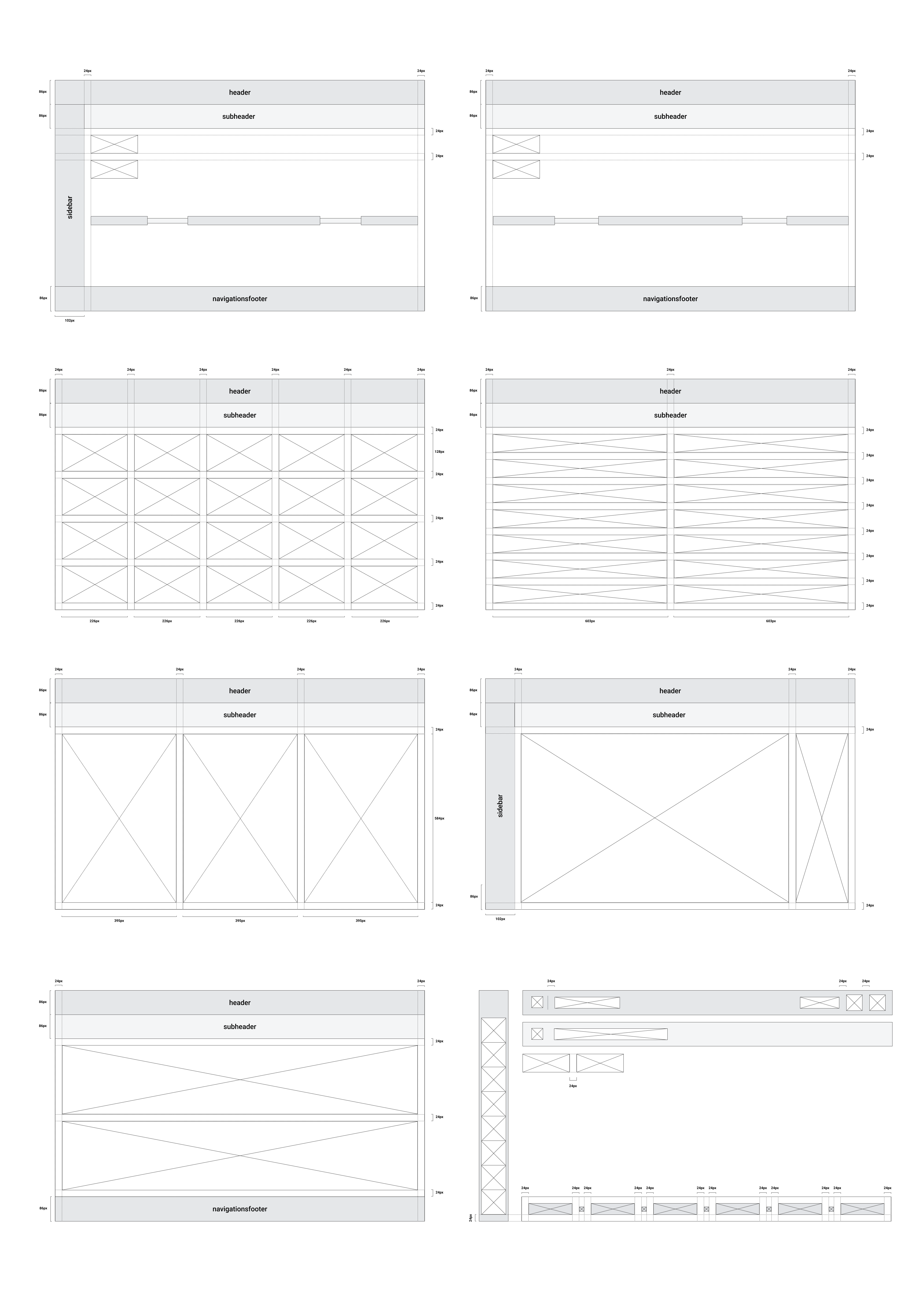
colours and typography
The interface employs sharp contrasts to highlight key features and controls, ensuring that users can navigate the software with ease. A dark background was chosen for the software interface, harmonizing with the machine’s dark exterior. This not only enhances readability and reduces eye strain but also reinforces the sleek, professional appearance of the machine
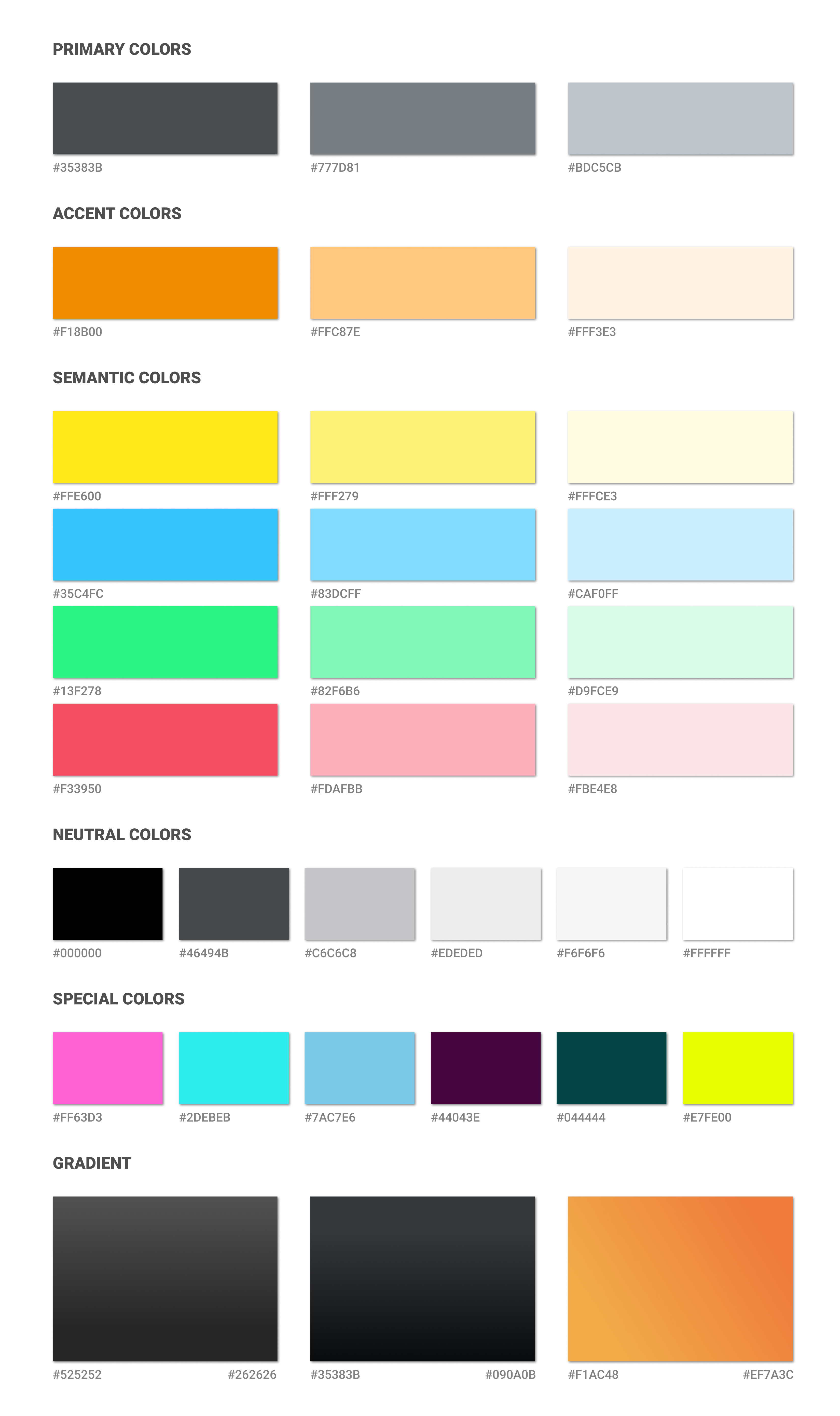
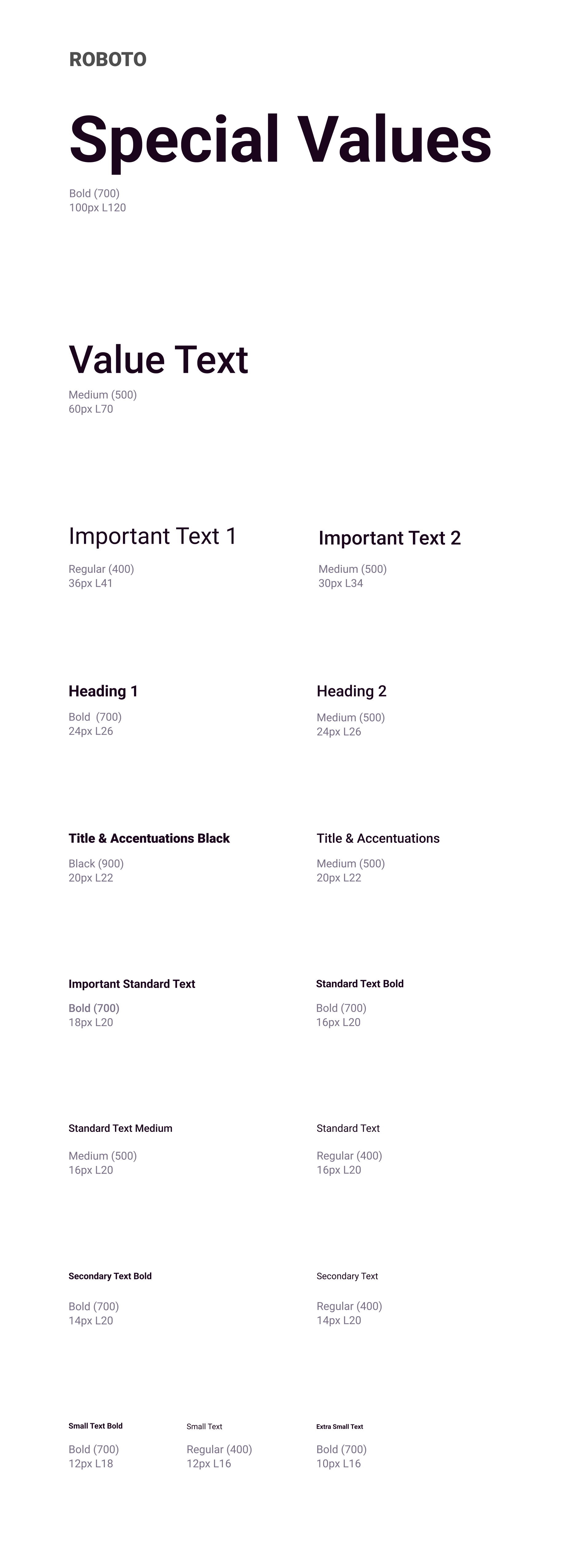